The blast furnace sludge is the waste of blast furnace ironmaking.In the blast furnace ironmaking process, impurities in iron ore, such as lead and zinc were restored, and to form steam at high temperatures, with ore, coke, fluxes and blast furnace gas was brought outside, then through the furnace gas dust purification system to catch removed. Coal gas gravity dust and fine dust of the dust removal system composed of two segments, the trap down in the first paragraph of the coarse particle dust dry is heavy dust; the second paragraph of fine dust and dry type bag filter or wet cleaning system. The drying type dedusting of drying fine-grained dust been known as bag filters dust (blast furnace dust, fine dust), The wet dust that obtained after precipitation treatment sludge been known as blas furnace sludge.
Blast furnace sludge primarily composed of iron oxide and carbon, also contains a small amount of zinc, bismuth, lead etc nonferrous metal. The blast furnace sludge/dust recycling, not only enable the valuable mineral resources To recycle, you can also reduce the dust pollution to the environment.
After numerous experiments, the blast furnace sludge/dust mix the sintered ore then briquetting by blast furnace sludge briquette machine,briquettes can be sintered in furnace, making full use of iron and carbon in sludge, to reduce energy consumption,reduce the cost of sintering.In addition, the blast furnace dust without additional processing, you can use the cheap coal as reducing agent and fuel, through briquetting by high pressure briquette machine, directly smelting on the furnace, it can be obtained more than 90% of the direct reduction iron.
Blast furnace gas sludge is mixed with iron ore concentrate powder and some binder, as 0.8 : 1 : 0.018 ratio, blend then go into high pressure briquette press machine to briquetting, the briquettes produced can roast in furnace The roasting temperature is 1330-1360 ℃, 50-60min roasting time, under the condition of 30-40mm fabric thickness, it can reach TFe75%-80%,MFe 60-70%, MR80-90%,C1-2%, S0.50%-0.60%.
Zhongzhou blast furnace sludge briquette machine is specifically designed for briquetting blast furnace sludge etc powdered materials, it has high productivity, high degree of automation, production efficiency,low failure rate, easy maintenance, so Zhongzhou blast furnace sludge/dust briquette machine was welcomed by many enterprises at home and abroad.
The flow chart of blast furnace sludge briquettes production line:
1, Hopper silo, uniform quantitative material to the horizontal two-shafts mixer.
2, Blender,also named liquid mixer, it is used for liquefied adhesive (if you use powdered adhesives, you can choose the dry powder feeder.)
3,The horizontal two-shaft mixer, full mixing raw materials, adhesives, water. The adhesives should uniform distribution among raw materials in order to achieve better thermal strength, briquettes is hard and better.
4, blast furnace sludge/dust briquette machine is the core of whole production line, it press mixing materials into briquettes, the briquettes' size and shape can be customized, zhongzhou can produce various shapes of rollers.
6, vertical dryer, drying the wet briquettes from briquette machine,the briquettes can be drying to 3% water content, finished briquettes will put in storage or packaged. 7, belt conveyor, connected to devices, it is guanrantee for the whole blast furnace sludge briquettes production line to realizes full automation.
The requirements for raw materials of blast furnace sludge briquettes production:
1, the particle size of the raw material should be between 0-5mm.
2, can not contain impurities, especially large metal. Such as nails, or iron, rocks, it very likely damage roller and spindle.
3, the feeding of whole produciton line should be stable, even, ensure workloads of briquette machine stable, to get high efficiency of production.
Zhongzhou company based on metallurgical briquette pressure equipment technical services, to create maximum value for clients, The blast furnace sludge briquette machine we produced has the high pressure, high finished product rate, high strength, fully meet the requirements of the operation of converter steelmaking, cost reduction for the production practice of converter smelting, optimized operation,shorten the smelting practice, speed up the rhythm of steel making, create the conditions for the realization of maximum benefit, we sincerely welcome all steel enterprises to explore, mutual benefit and win-win.
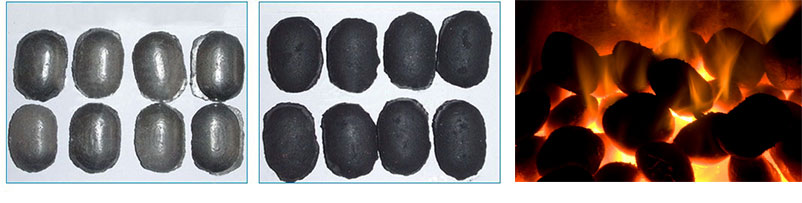